Your cart is currently empty!
SayPro Tasks to Be Done for the Period: Week 2 Goal
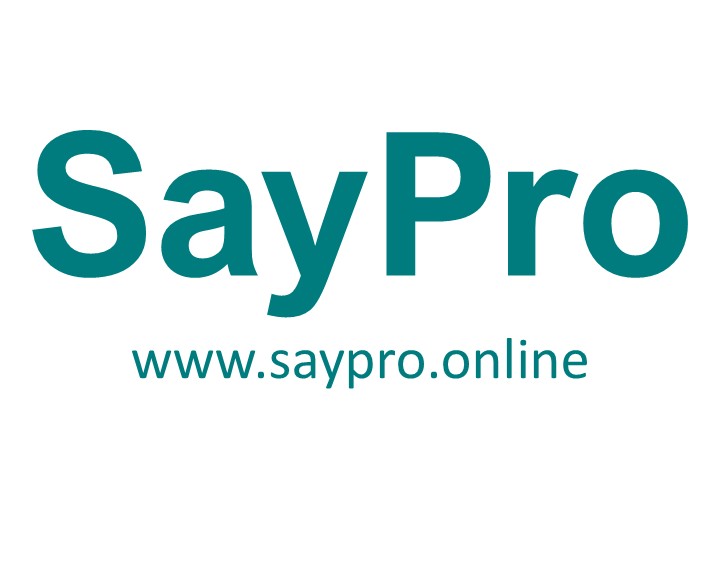
SayPro Monthly January SCMR-13: SayPro Monthly Printing: Use High Resolution Printing for Clear and Vibrant Visuals by SayPro Brand Material Office under SayPro Marketing Royalty
Goal: Ensure that there are no technical issues or errors in the files before sending them to the printer. This is part of the SayPro Monthly January SCMR-13: SayPro Monthly Printing initiative. The files will be printed under SayPro Brand Material Office with high-resolution quality for clear and vibrant visuals.
1. Review and Finalize the Files
- Objective: Double-check all files to ensure they are finalized for printing, free from errors, and formatted correctly.
- Actions:
- Check Layout Consistency: Review all design layouts (margins, spacing, fonts, images, color schemes) for consistency across the entire document.
- Check Resolution: Ensure that all images are in high resolution (300 DPI) for clear and vibrant printing. Any images below 300 DPI must be replaced or adjusted.
- Color Settings: Confirm the color settings are in CMYK mode for print compatibility (ensure no RGB colors are included).
- Proofreading: Review all content (text, headings, subheadings, captions) for grammar, punctuation, spelling, and factual errors.
- Review Text Flow: Ensure there is no overrun of text and the content fits within the designated space for the layout without distortion.
- Actions:
2. Quality Assurance (QA) Testing
- Objective: Conduct a comprehensive quality check to identify any technical flaws before final submission to the printing department.
- Actions:
- Proof Print: Perform a test print of a small section or single page to identify any issues with colors, clarity, and formatting.
- Font Verification: Verify that all fonts are embedded and compatible with the printer (check that no fonts are missing or substituted incorrectly).
- Image Sharpness: Inspect images on screen at actual print size to confirm there are no pixelation issues or blurriness.
- Check Bleed and Cut Lines: Ensure that any bleed areas are correctly set up (extend past the trim line) and the cut lines are properly aligned.
- File Format Confirmation: Ensure the file is in the correct format for the printer (PDF, TIFF, or any other required format). Convert all files to a print-ready format.
- Actions:
3. Cross-Department Collaboration
- Objective: Ensure communication and smooth workflow with the marketing, design, and printing teams to avoid any discrepancies or delays.
- Actions:
- Design Team Collaboration: Communicate with the design team to confirm that all elements of the layout are in line with the final design expectations.
- Printing Team Coordination: Contact the printing team to verify file specifications (paper type, print quantity, binding methods) and confirm that the design will print as expected.
- Feedback Incorporation: Address any last-minute feedback from internal stakeholders (marketing, sales, etc.) to ensure their requests are incorporated into the final print-ready files.
- Actions:
4. Verify Print Materials and Specifications
- Objective: Ensure all print materials (papers, ink, finishes) are selected according to the project requirements for high-quality results.
- Actions:
- Paper Type Verification: Confirm the correct type and weight of paper is selected for printing (e.g., matte, glossy, or premium finish).
- Ink and Finish Selection: Ensure that the chosen ink types and finishes (e.g., UV coating, spot gloss) align with the project’s visual and tactile goals.
- Confirm Quantity: Verify the total quantity of prints to ensure it matches the order and any future needs (e.g., for distribution or storage).
- Actions:
5. Ensure Delivery Timeline Compliance
- Objective: Guarantee that files are delivered to the printer within the agreed timeframe, ensuring smooth production without delays.
- Actions:
- File Submission Deadline: Ensure the finalized files are submitted to the printer by the established deadline (e.g., end of Week 2).
- Follow-up: Send a confirmation email to the printing team to ensure they have received the files and to address any immediate questions or concerns.
- Monitor Production Schedule: Keep track of the production schedule to confirm that the prints are completed and ready for delivery within the required timeframe.
- Actions:
6. File Backup and Documentation
- Objective: Maintain organized documentation of the finalized print files and related communications for future reference and reprints.
- Actions:
- File Backup: Back up all final print-ready files in a secure location (cloud storage, external hard drive).
- File Documentation: Create a folder containing the original design files, print specifications, feedback logs, and communication history for archiving.
- Print Run Tracking: Document the print quantity, paper type, ink selection, and finish for future reprints or adjustments.
- Actions:
Completion Goal for Week 2: By the end of Week 2, the final print files should be free of any technical issues, formatted correctly, proofed, and submitted to the printing team for production. There should be no outstanding errors or revisions needed before printing commences.
Leave a Reply
You must be logged in to post a comment.