Your cart is currently empty!
SayPro Operational Efficiency: Reduce operational costs by 5% through process improvements
SayPro is a Global Solutions Provider working with Individuals, Governments, Corporate Businesses, Municipalities, International Institutions. SayPro works across various Industries, Sectors providing wide range of solutions.
SayPro Email: info@saypro.online Call/WhatsApp: + 27 84 313 7407
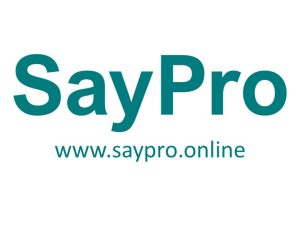
To achieve a 5% reduction in operational costs at SayPro through process improvements, we need a strategic approach focused on enhancing efficiency, streamlining workflows, optimizing resources, and eliminating waste. The goal is to identify areas where operational costs can be minimized while maintaining or improving output quality. Here’s a comprehensive Operational Efficiency Improvement Plan for SayPro.
SayPro Operational Efficiency Improvement Plan
Objective: Reduce operational costs by 5% through process improvements across various departments.
Timeline: Next Quarter (3 months)
1. Analyze Current Operations and Baseline Costs
A. Review Financial Statements
- Identify Major Cost Drivers: Review financial data to identify areas with the highest costs, such as labor, raw materials, overhead, and third-party services.
- Cost Allocation: Break down costs by department, process, and activity to understand where inefficiencies may exist (e.g., procurement, supply chain, administrative overhead).
B. Process Mapping & Time Audits
- Map Key Processes: Create detailed process maps for core business functions (e.g., customer service, product development, procurement, order fulfillment).
- Time Tracking & Productivity Analysis: Use time-tracking tools (e.g., Toggl, Clockify) to assess the time spent on key tasks, identify bottlenecks, and areas for improvement in productivity.
2. Identify Areas for Process Improvement
A. Workflow Optimization
- Eliminate Bottlenecks: Analyze each key business process and identify bottlenecks or areas of redundancy. Use value stream mapping to visualize inefficiencies and develop strategies to streamline operations.
- Automation of Repetitive Tasks: Identify processes that can be automated (e.g., payroll, customer support ticketing, data entry). Implement tools like Zapier, UiPath, or Monday.com to automate manual tasks.
- Consolidation of Tasks: Consolidate tasks that are redundant or could be done simultaneously (e.g., combine administrative tasks or communication between departments).
B. Lean Six Sigma Implementation
- Eliminate Waste: Use Lean principles to identify and eliminate non-value-added activities (e.g., unnecessary steps in workflows, excessive inventory).
- Reduce Variability: Use Six Sigma techniques to improve consistency in key processes (e.g., reducing errors in customer orders, improving service delivery times).
- Kaizen (Continuous Improvement): Introduce a Kaizen culture, where employees are encouraged to regularly suggest improvements in processes and suggest ways to cut costs.
C. Optimize Resource Utilization
- Labor Optimization: Assess the effectiveness of your labor force. Consider implementing capacity planning to ensure you have the right number of employees working at the right time, reducing overtime and idle time.
- Outsourcing & Offshoring: Review non-core activities that could be outsourced (e.g., IT support, HR services, logistics) to reduce internal labor costs while maintaining quality.
- Equipment Utilization: Optimize the use of machinery and equipment by maintaining a schedule for preventative maintenance to avoid breakdowns and downtime.
3. Cost Reduction in Key Departments
A. Procurement and Supply Chain Efficiency
- Negotiate with Suppliers: Revisit contracts with suppliers and vendors to negotiate better rates, bulk discounts, or favorable payment terms.
- Inventory Management: Implement just-in-time inventory to reduce inventory holding costs. Use demand forecasting tools to minimize overstocking.
- Reduce Waste: Implement waste-reduction strategies such as reducing packaging materials, optimizing shipping methods, or finding ways to repurpose unused materials.
B. Marketing & Advertising
- Digital Marketing Optimization: Evaluate the performance of marketing channels (e.g., PPC ads, social media campaigns, email marketing) and identify opportunities for cost-effective targeting and segmentation.
- Outsource Creative Work: Instead of maintaining an in-house creative team, consider outsourcing content creation to freelancers or specialized agencies to reduce overhead costs.
- Customer Acquisition Cost (CAC) Reduction: Focus on improving customer retention strategies to lower the cost of acquiring new customers. Invest in referral programs, loyalty programs, and customer satisfaction improvements to reduce churn.
C. Customer Support & Service
- Self-Service Support: Develop a comprehensive knowledge base, FAQs, or chatbot system to reduce the volume of support requests and lower support costs.
- Customer Support Automation: Implement AI-powered tools or automatic ticketing systems to handle routine queries and ensure faster response times.
- Outsource Non-Critical Support: Consider outsourcing non-critical customer service functions to lower-cost regions while maintaining service quality.
D. IT and Infrastructure
- Cloud Computing: Migrate to cloud-based services (if not already done) to reduce IT infrastructure costs, improve scalability, and eliminate expensive on-premise hardware and maintenance costs.
- Software Licensing Audit: Review software subscriptions and licenses to ensure you’re not paying for unused tools or redundant software.
- Centralized IT Support: Consider consolidating IT support tasks (e.g., network monitoring, helpdesk, system maintenance) into a single team or outsourced service to reduce costs.
4. Employee Training & Engagement
A. Cross-Training Employees
- Develop Cross-Training Programs: Cross-train employees across different departments to improve versatility and ensure smooth workflow during peak times, vacations, or when an employee is absent. This reduces the need to hire additional temporary staff.
- Continuous Learning & Development: Offer employees training in skills that improve operational efficiency (e.g., process improvement, project management, or automation tools) to empower them to identify inefficiencies and implement improvements.
B. Employee Empowerment & Feedback
- Encourage Problem Solving: Empower employees to identify inefficiencies and suggest cost-saving measures. Develop a feedback loop for employees to report inefficiencies and reward them for actionable suggestions.
- Recognition of Cost-Saving Initiatives: Recognize employees who contribute ideas that help save costs (e.g., reducing material wastage, optimizing workflows). Offer incentives like bonuses or public recognition.
5. Implement Technology Solutions
A. Implement Enterprise Resource Planning (ERP)
- Centralized System: Implement or upgrade an ERP system (e.g., SAP, Oracle NetSuite) to centralize financials, inventory, HR, and supply chain management. An ERP system can automate processes, reduce redundancies, and give you real-time data to make smarter decisions.
- Data-Driven Decision Making: Use ERP data to analyze operational efficiency and pinpoint areas to improve or cut costs. Use dashboards for easy tracking of key performance indicators (KPIs) across departments.
B. Use Predictive Analytics
- Demand Forecasting: Implement predictive analytics tools to forecast demand more accurately, which can help reduce inventory costs, minimize stockouts, and avoid overproduction.
- Employee Scheduling: Use predictive scheduling tools to optimize employee shift schedules, ensuring that staffing aligns with workload demand to reduce overtime and under-utilization.
6. KPIs to Track Operational Efficiency Progress
Metric | Description | Target | Measurement Method |
---|---|---|---|
Operational Cost Reduction | Percentage reduction in overall operational costs. | 5% reduction | Financial Statements, Monthly Reports |
Process Improvement Time | Time saved by process optimizations and automation. | 10% reduction in process time | Time Audits, Process Mapping |
Employee Productivity | Measure output per employee, after improvements. | 5% increase | Employee Performance Reviews, KPIs |
Customer Satisfaction | Satisfaction rates, reflecting operational improvements. | 90% or higher | Customer Satisfaction Surveys (CSAT) |
Inventory Turnover Rate | Measure inventory efficiency to minimize holding costs. | Increase by 10% | Inventory Reports, ERP System |
Supplier Cost Reduction | Reduction in procurement costs through better negotiation. | 5% reduction | Procurement Reports, Supplier Contracts |
Automation Adoption Rate | Measure adoption of automation tools across departments. | 30% increase | Internal Reports, Software Analytics |
7. Timeline for Implementation
Task | Responsible Party | Start Date | End Date |
---|---|---|---|
Analyze Operational Costs | Finance & Operations Teams | 2025-05-01 | 2025-05-07 |
Process Mapping & Time Audits | Operations & HR Teams | 2025-05-01 | 2025-05-15 |
Automation Implementation | IT & Operations Teams | 2025-05-10 | 2025-06-30 |
Cross-Training Programs | HR & Department Managers | 2025-05-15 | Ongoing |
ERP & Analytics Integration | IT & Data Teams | 2025-05-01 | 2025-06-30 |
Supplier Negotiation & Cost Analysis | Procurement Team | 2025-05-01 | 2025-05-31 |
Conclusion & Next Steps
By optimizing workflows, leveraging technology, improving employee efficiency, and focusing on cost-effective practices, SayPro can achieve its goal of reducing operational costs by 5%. Regular tracking of the key performance indicators (KPIs) will allow for adjustments and ensure progress toward this goal.
Would you like me to dive deeper into any of these areas or provide more specific recommendations?
Leave a Reply
You must be logged in to post a comment.