Your cart is currently empty!
SayPro Quality Assurance Checklist
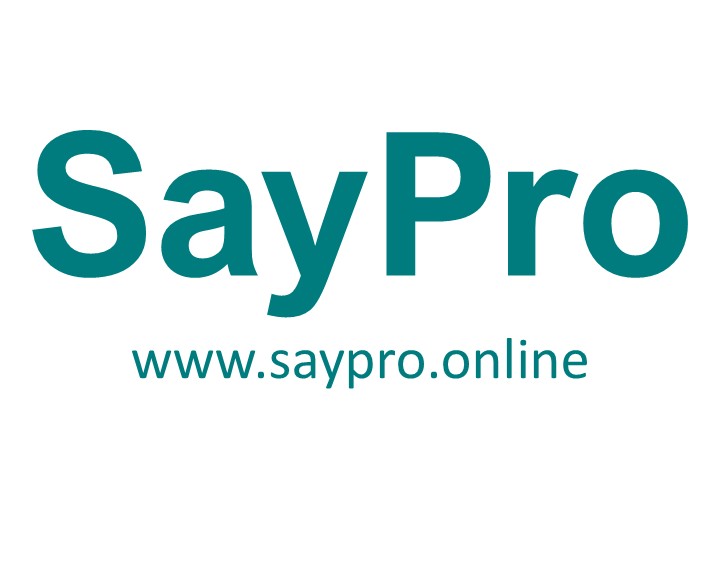
SayPro Monthly January SCMR-13 SayPro Monthly Printing: Select appropriate paper stock and finish by SayPro Brand Material Office under SayPro Marketing Royalty SCMR
SayPro SCMR-13 – Printing Process: Collaborating with Printers
Main Theme:
Ensuring seamless and efficient collaboration with print partners to produce high-quality SayPro materials that reflect the SayPro brand standards and support all business units and programs effectively.
Section 1: Introduction to SayPro’s Printing Philosophy
- The role of printed materials in SayPro’s brand presence
- Importance of consistency, quality, and timeliness
- Overview of the SayPro Brand Material Office responsibilities
Section 2: SayPro’s Printing Workflow Overview
- Step-by-step process from design to delivery
- Internal coordination with the Brand Material Office
- Timeline benchmarks and turnaround expectations
- Standard operating procedures (SOPs) for submission to printers
Section 3: Selecting the Right Printing Partner
- Approved SayPro printing vendors and evaluation criteria
- Vetting process: quality control, reliability, and compliance
- Long-term partnership strategies and vendor accountability
- Ethical sourcing and environmental compliance checks
Section 4: Selecting Appropriate Paper Stock and Finish
- Overview of paper types (glossy, matte, uncoated, recycled)
- When to use premium vs. standard stock for different campaigns
- Branding considerations in finish (e.g., UV spot, lamination, embossing)
- Paper stock selection per SayPro material type:
- Training manuals
- Brochures
- Flyers
- Posters
- Product packaging inserts
- Guidance from SayPro Brand Material Office for official projects
Section 5: File Preparation and Pre-Press Standards
- SayPro design file checklist: bleed, crop marks, color mode (CMYK)
- Format requirements (PDF/X standards, resolution minimums)
- Pre-press approval procedure
- How to submit final print files to vendors
- SayPro template usage and digital asset management
Section 6: Color Matching and Brand Fidelity
- SayPro color palette (Pantone + CMYK/RGB equivalence)
- Maintaining brand color fidelity across different materials
- Proofing process and spot-check protocols
- Printer test runs and approval process
- SayPro Brand Quality Control (QC) sheet
Section 7: Print Production Timelines
- Typical lead times for various materials
- Rush order guidelines and cost considerations
- Coordinating around SayPro event calendars and campaign schedules
- Workflow scheduling in Asana/Trello for transparency
Section 8: Collaboration and Communication Protocols
- Designation of SayPro print liaison officers
- Best practices for working with printers (calls, revisions, approvals)
- Clear communication of specs and expectations
- Feedback loops and issue resolution escalation process
Section 9: Delivery, Distribution, and Post-Print Inspection
- Receiving and inspecting printed goods
- Storage and warehousing protocols
- Distribution via SayPro Logistics or external partners
- Reporting defective runs or inconsistencies
- Post-project debrief and vendor performance review
Section 10: Sustainability and Innovation in Printing
- SayPro’s commitment to sustainable print practices
- Recycled materials, soy-based inks, and low-VOC finishes
- QR code integration and print-to-digital transitions
- Experimenting with AR and NFC-enabled print experiences
Section 11: SayPro Monthly SCMR Printing Campaign Examples
- Breakdown of January’s SCMR-13 print run:
- Material types
- Chosen paper stocks and finishes
- Vendor partnerships
- Timeline success
- Lessons learned
Section 12: Appendices and Tools
- Approved paper swatch samples with finish annotations
- SayPro print specification templates (editable)
- Sample vendor briefing document
- SayPro Print QC checklist
- Paper and finish reference guide
Leave a Reply
You must be logged in to post a comment.