Your cart is currently empty!
SayPro Quality Control and Distribution
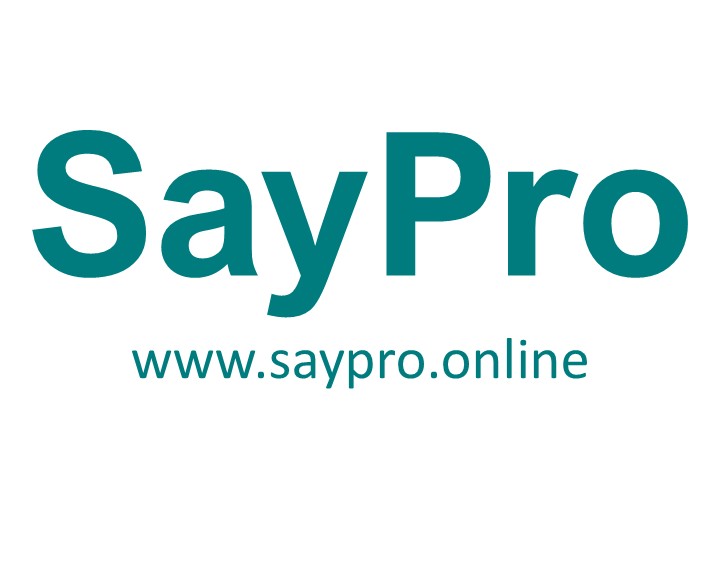
SayPro Monthly January SCMR-13 SayPro Monthly Printing: Choose high quality paper for a professional feel by SayPro Brand Material Office under SayPro Marketing Royalty SCMR
Overview
SayPro is committed to ensuring high-quality print materials that align with brand standards and design specifications. The SayPro Quality Control and Distribution process oversees every stage of printing to maintain consistency in paper quality, color fidelity, and alignment, ensuring all printed materials meet professional standards.
Quality Control Process
1. Pre-Press Quality Checks
Before printing begins, SayPro enforces strict quality control measures, including:
- Design Proofing: Ensuring that digital files are correctly formatted and optimized for printing.
- Color Accuracy: Verifying that colors match brand guidelines and digital proofs using Pantone or CMYK standards.
- Paper Selection: Choosing the appropriate high-quality paper for a professional feel, as recommended by the SayPro Brand Material Office under SayPro Marketing Royalty SCMR.
2. Printing Phase Monitoring
During the printing process, SayPro ensures:
- Consistency in Paper Quality: Each batch of paper is checked for uniformity in thickness, texture, and finish.
- Color Fidelity: Regular calibration of printing machines to maintain color accuracy across all prints.
- Alignment & Precision: Verifying that print layouts are properly aligned and free from distortions or misprints.
3. Post-Printing Inspection
Once printing is complete, additional quality control measures include:
- Physical Examination: Inspecting printed materials for any defects, smudging, or misalignment.
- Batch Sampling: Conducting random checks on bulk prints to ensure consistent quality.
- Finishing and Binding: Reviewing lamination, binding, and other finishing touches to enhance durability and presentation.
Distribution Process
1. Packaging and Handling
- Protective Wrapping: Using high-quality, eco-friendly materials to prevent damage during transit.
- Batch Labeling: Clearly labeling shipments for easy identification and tracking.
2. Logistics and Delivery
- Efficient Shipping Channels: Utilizing trusted courier services for timely distribution.
- Inventory Management: Maintaining a well-organized system to track printed materials and prevent shortages or overstocking.
- Customer Confirmation: Ensuring clients receive their materials in excellent condition and on schedule.
Commitment to Excellence
SayPro’s Quality Control and Distribution framework is designed to uphold the highest standards in printed material production. By enforcing rigorous checks at every stage, SayPro ensures that every printed product reflects the professionalism and excellence of the SayPro brand.
This process, detailed in SayPro Monthly January SCMR-13, serves as the benchmark for maintaining superior print quality and efficient distribution, solidifying SayPro’s reputation for excellence in branding and marketing materials.
Leave a Reply
You must be logged in to post a comment.