Your cart is currently empty!
SayPro Cost-effective printing solutions
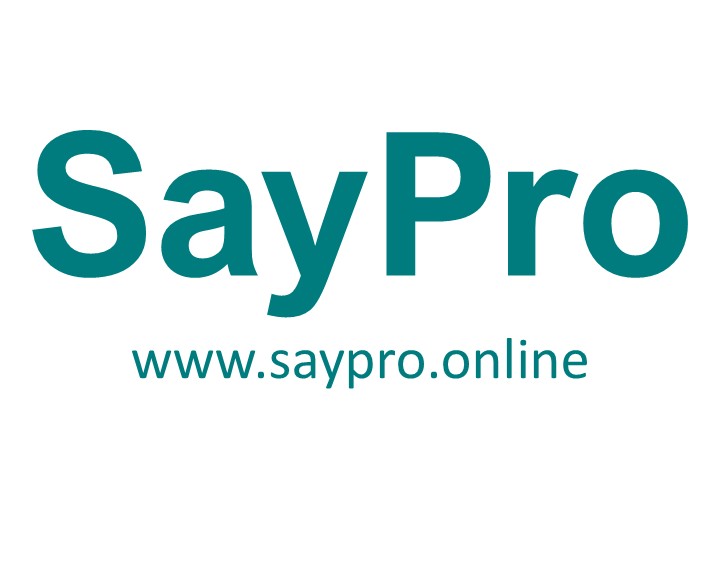
SayPro Monthly January SCMR-13 SayPro Monthly Printing: Select appropriate paper stock and finish by SayPro Brand Material Office under SayPro Marketing Royalty SCMR
SayPro SCMR-13: Quality Control in the Printing Process
SECTION 1: Introduction to SayPro Printing Standards
- 1.1 Overview of SCMR-13 and its role in brand consistency
- 1.2 Importance of printing quality in SayPro’s communication strategy
- 1.3 Responsibilities of the SayPro Brand Material Office
- 1.4 Monthly Printing Mandates – Summary from SayPro Monthly January
SECTION 2: Paper Stock and Finishing Standards
- 2.1 Selecting appropriate paper stock for different marketing materials
- 2.1.1 Business cards, brochures, flyers, banners, reports
- 2.1.2 Weight, texture, and color matching SayPro Brand Identity
- 2.2 Approved paper types by the SayPro Brand Material Office
- 2.3 Finishing options and their applications
- 2.3.1 Glossy vs. matte finish
- 2.3.2 Spot UV, lamination, embossing/debossing
- 2.3.3 Binding methods for reports and booklets
SECTION 3: Pre-Press Quality Control Procedures
- 3.1 File preparation and formatting checklist
- 3.1.1 Bleed, trim, safe zone specifications
- 3.1.2 CMYK color mode and resolution standards
- 3.2 Proofing procedures
- 3.2.1 Digital vs. physical proofs
- 3.2.2 Approval process by Brand Material Office
- 3.3 Font embedding and image licensing
- 3.4 Layout consistency with SayPro Brand Guidelines
SECTION 4: In-Press Quality Monitoring
- 4.1 Press checks – Visual inspections during print runs
- 4.2 Color calibration and consistency standards
- 4.2.1 Pantone color matching
- 4.2.2 Maintaining color fidelity across materials
- 4.3 Alignment and registration accuracy
- 4.4 Ink density and coverage controls
SECTION 5: Post-Press and Finishing Inspection
- 5.1 Quality inspection checklist after printing
- 5.1.1 Trim accuracy
- 5.1.2 Binding integrity
- 5.1.3 Finish application consistency
- 5.2 Packaging and delivery standards
- 5.2.1 Protective wrapping
- 5.2.2 Labeling and inventory tracking for distribution
- 5.3 Handling reprints and correcting defects
SECTION 6: Continuous Quality Improvement
- 6.1 Feedback loop from marketing and end users
- 6.2 Recording quality issues and corrective actions
- 6.3 Supplier evaluation and audits
- 6.4 Training and development for in-house and outsourced print staff
SECTION 7: Compliance and Documentation
- 7.1 Record-keeping of all print jobs and approvals
- 7.2 Monthly quality audits and summary reports
- 7.3 Archiving SayPro Monthly SCMR-13 quality reviews
- 7.4 Ensuring all materials align with SayPro Marketing Royalty SCMR directives
Leave a Reply
You must be logged in to post a comment.