Your cart is currently empty!
SayPro Operational Efficiency Analysis Template: A tool for identifying process inefficiencies and recommending improvements.
SayPro is a Global Solutions Provider working with Individuals, Governments, Corporate Businesses, Municipalities, International Institutions. SayPro works across various Industries, Sectors providing wide range of solutions.
Email: info@saypro.online Call/WhatsApp: + 27 84 313 7407
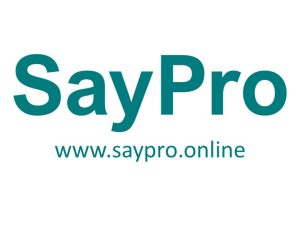
SayPro Operational Efficiency Analysis Template
The Operational Efficiency Analysis Template is designed to identify areas of inefficiency within operational workflows, analyze their impact on overall performance, and recommend strategies for process improvement. It provides a structured approach to evaluating existing operations and offers actionable solutions to streamline processes, reduce costs, and enhance productivity.
1. Analysis Overview
Date of Analysis:
Enter the date the operational efficiency analysis was conducted.
Department/Area Evaluated:
Specify the department or operational area being analyzed (e.g., Customer Support, Marketing, Production, etc.).
Analysis Lead/Team:
Name of the individual or team responsible for conducting the analysis.
2. Operational Process Review
Process Name:
Enter the name of the operational process being evaluated (e.g., order fulfillment, customer onboarding, project management, etc.).
Process Description:
Briefly describe the purpose and scope of the process under review.
Key Stakeholders:
List key individuals or teams involved in the process (e.g., operations team, customer support, IT, etc.).
Process Flow:
Provide a high-level description or flowchart of the process being analyzed.
3. Efficiency Evaluation Criteria
Criteria for Assessment:
Outline the specific criteria used to evaluate the operational efficiency of the process, such as time, cost, resource usage, quality, and customer satisfaction.
Criteria | Description | Measurement Method |
---|---|---|
Time Efficiency | How long the process takes from start to finish. | Time logs, process timestamps |
Cost Efficiency | Cost associated with executing the process. | Budget and expense tracking |
Resource Utilization | How well resources (human, material, financial) are allocated. | Resource tracking tools, staffing records |
Quality Control | The consistency and quality of outputs generated by the process. | Defects per unit, quality checks |
Customer Satisfaction | How well the process satisfies customer expectations. | Surveys, NPS scores |
Process Flexibility | The process’s ability to adapt to changes in demand or scope. | Capacity analysis, feedback from teams |
4. Current Performance Metrics
Time Performance:
Describe the average time required to complete the process and how it compares to industry standards or internal benchmarks.
Step in Process | Average Time | Industry Benchmark | Comments |
---|---|---|---|
Initial Inquiry Response | 4 hours | 2 hours | Time spent on research causes delays. |
Order Processing | 24 hours | 18 hours | Delays due to manual steps in the process. |
Final Delivery/Execution | 5 days | 4 days | Shipping delays due to lack of coordination. |
… | … | … | … |
Cost Performance:
Evaluate the costs associated with executing the process, comparing actual expenses with budgeted figures or industry norms.
Step in Process | Actual Cost | Budgeted Cost | Variance | Comments |
---|---|---|---|---|
Initial Inquiry Handling | $500 | $400 | +$100 | Additional personnel hired for support. |
Order Fulfillment | $2,000 | $1,800 | +$200 | Shipping costs increased due to delays. |
Final Delivery/Execution | $1,500 | $1,200 | +$300 | Packaging costs increased due to packaging errors. |
… | … | … | … | … |
Resource Utilization:
Evaluate how well human and material resources are utilized during the process, identifying any overuse or underuse of resources.
Resource | Utilization | Optimal Utilization | Comments |
---|---|---|---|
Staff Hours | 80% | 100% | Underutilized in non-peak hours. |
Inventory Stock | 90% | 80% | Some overstocking, leading to excess storage costs. |
IT Systems/Software | 70% | 100% | System downtime impacting productivity. |
… | … | … | … |
5. Process Bottlenecks and Inefficiencies
Bottleneck Identification:
List any points in the process where delays or inefficiencies are occurring. These bottlenecks may be related to time, cost, resources, or other factors.
Bottleneck Step | Impact | Root Cause | Solution Proposed |
---|---|---|---|
Initial Inquiry Response | Delayed response time leading to customer dissatisfaction | Inadequate automation of response system. | Implement automated email responses. |
Order Processing | Increased processing time and manual errors | Lack of integration between systems. | Integrate order management and CRM systems. |
Final Delivery/Execution | Delayed shipments, customer complaints | Lack of coordination between teams (logistics, production). | Improve communication between departments. |
… | … | … | … |
6. Recommendations for Process Improvement
Recommendation 1: Automation of Manual Tasks
Automate repetitive and manual tasks such as data entry, customer responses, and report generation to reduce time spent and errors.
- Impact: Reduced processing time and error rates.
- Cost: Low to moderate (depending on the system implemented).
- Timeline: 3 months.
Recommendation 2: Enhance Resource Allocation
Review staffing levels and redistribute human resources to improve efficiency during peak periods.
- Impact: More efficient use of available resources, reduced overtime costs.
- Cost: Low.
- Timeline: Immediate.
Recommendation 3: Improve Cross-Departmental Communication
Establish regular check-ins and a centralized communication system between departments (e.g., marketing, logistics, production) to avoid delays and ensure smoother execution of tasks.
- Impact: Faster issue resolution, reduced delays.
- Cost: Low.
- Timeline: 2 months.
Recommendation 4: Implement Performance Monitoring Systems
Introduce real-time monitoring and reporting tools to track KPIs and address inefficiencies before they impact the overall process.
- Impact: Proactive identification of issues, improved decision-making.
- Cost: Moderate (for software tools).
- Timeline: 6 months.
7. Risk and Challenges in Implementing Recommendations
Recommendation | Risk/Challenge | Mitigation Strategy |
---|---|---|
Automation of Manual Tasks | Resistance from staff or difficulty in adapting to new systems | Provide training and gradually phase in automation. |
Enhance Resource Allocation | Budget limitations to hire additional staff | Cross-train existing employees to handle multiple roles. |
Improve Cross-Departmental Communication | Lack of buy-in from all teams | Ensure leadership endorsement and set clear communication protocols. |
Implement Performance Monitoring | Initial investment cost for tools and systems | Justify the investment with data on potential productivity gains. |
8. Conclusion and Next Steps
Summarize the findings of the operational efficiency analysis, highlight the key areas requiring improvement, and outline the next steps for implementing the recommended changes.
9. Sign-Off
Analyst Name | Position | Signature | Date |
---|---|---|---|
[Analyst Name] | [Position Title] | [Signature] | [Date] |
[Department Head Name] | [Position Title] | [Signature] | [Date] |
… | … | … | … |
This SayPro Operational Efficiency Analysis Template offers a detailed structure for evaluating and improving operational processes. By identifying inefficiencies, measuring key performance criteria, and recommending actionable solutions, SayPro can improve productivity, reduce costs, and ensure better alignment with strategic goals.
Leave a Reply
You must be logged in to post a comment.