Your cart is currently empty!
SayPro Printing Quality Reports
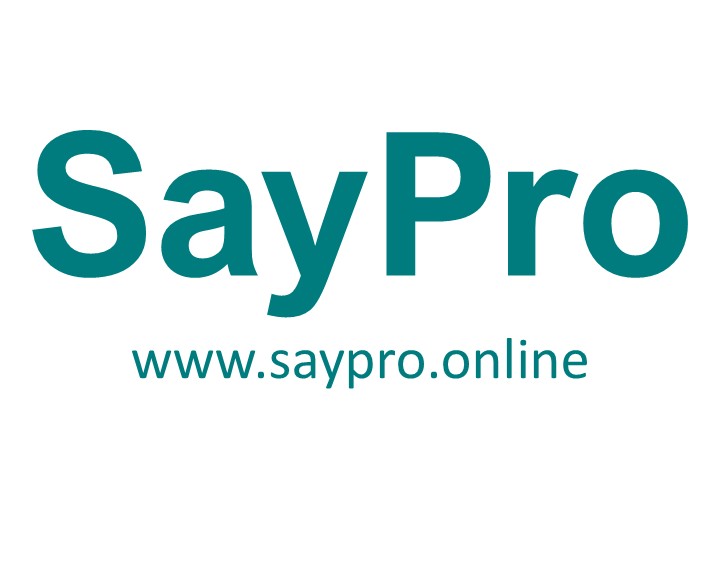
SayPro Monthly January SCMR-13 SayPro Monthly Printing: Select appropriate paper stock and finish by SayPro Brand Material Office under SayPro Marketing Royalty SCMR
SayPro – Information and Targets for the Quarter
Department: SayPro Marketing Royalty (SCMR)
Unit: SayPro Brand Material Office
Focus Area: Printing Quality, Material Standards, and Process Monitoring
Reference Documents:
- SCMR-13: SayPro Monthly January Report
- SCMR: SayPro Monthly Printing and Quality Management
1. Printing Quality Reports
Objective:
To improve and standardize the quality of all printed materials used across SayPro’s marketing and branding campaigns.
Target Outcomes for the Quarter:
- Ensure 100% compliance with SayPro brand quality standards in all printed materials.
- Reduce quality issues by at least 30% compared to the previous quarter.
- Implement a structured tracking and resolution system for any reported printing issues.
Action Points:
a) Recording Quality Issues:
- All departments must log any identified print quality issues in the centralized quality tracking system.
- Each entry should include:
- Description of the issue (e.g., color mismatch, blurred text, paper tears).
- Affected material (e.g., brochures, training manuals, flyers).
- Date of discovery.
- Responsible supplier or internal unit.
b) Resolution & Follow-Up:
- Issues logged must be resolved within 5 business days.
- The SayPro Brand Material Office will investigate the root cause and assign responsibility.
- Corrective actions (e.g., reprinting, supplier change, paper upgrade) must be documented and verified.
- Monthly reporting on resolution statistics to be submitted in the SCMR Monthly Report.
c) Quarterly Review Metrics:
- Total number of issues reported
- Resolution turnaround time (average in days)
- Recurring issues and supplier performance
- Satisfaction score from internal SayPro stakeholders
2. SayPro Monthly Printing Standards
Objective:
Ensure all printed materials uphold the prestige of the SayPro brand by maintaining consistency in material quality and finish.
Material Selection Guidelines:
- Paper Stock:
- Use premium-grade, eco-certified paper for all public-facing materials.
- Minimum 170gsm for brochures, 250gsm for covers.
- Internal materials may use 120gsm unless otherwise required.
- Finish:
- Gloss finish for promotional material; matte for professional communications (e.g., reports, whitepapers).
- Use UV spot finishes on logos and headings for high-impact branding.
- Consistency:
- All materials to follow SayPro’s Brand Identity Manual.
- Any deviations must be approved in writing by the SayPro Brand Material Office.
3. Roles and Responsibilities
Team/Department | Responsibility |
---|---|
SayPro Brand Material Office | Define and approve paper types, finishes, and branding for all printed material |
SCMR Quality Unit | Monitor, log, and follow up on print quality issues |
External Print Vendors | Comply with SayPro print specifications; address errors and reprints if needed |
All Internal Teams | Report any quality issues immediately and support investigations |
Conclusion and Next Steps
SayPro’s focus this quarter is on eliminating repeat print quality issues and ensuring that all printed branding reflects the professionalism and integrity of the organization. The structured reporting and material approval process will lead to:
- Better cost control through fewer reprints.
- Improved brand consistency.
- Higher satisfaction among stakeholders and partners.
The next SCMR Monthly Report (February) will include an updated table of reported issues, response actions, and compliance scores across departments.
Leave a Reply
You must be logged in to post a comment.