Your cart is currently empty!
SayPro Production Collaboration: Work with the production team to ensure the packaging designs are executed correctly and on schedule.
SayPro is a Global Solutions Provider working with Individuals, Governments, Corporate Businesses, Municipalities, International Institutions. SayPro works across various Industries, Sectors providing wide range of solutions.
Email: info@saypro.online Call/WhatsApp: + 27 84 313 7407
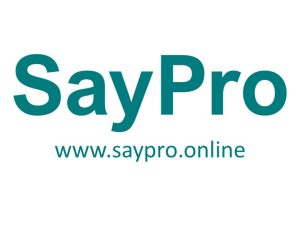
SayPro Production Collaboration
1. Introduction
The SayPro Production Collaboration phase is the final step in bringing the packaging design to life. In this phase, the design team works closely with the Production Team to ensure that the packaging is manufactured correctly, efficiently, and on schedule. The objective is to seamlessly translate the approved design into actual packaging while addressing any production challenges, ensuring quality control, and meeting deadlines.
2. Key Objectives of Production Collaboration
The primary objectives of the collaboration between the design team and production team are:
- Ensure Design Accuracy: Ensure that the final packaging design is produced exactly as planned, including all colors, dimensions, and material specifications.
- Address Production Constraints: Work with the production team to identify any constraints (e.g., material availability, manufacturing limitations) and adjust the design accordingly without compromising quality or functionality.
- Meet Deadlines: Stay on schedule to ensure the packaging is ready for product launches and distribution.
- Maintain Quality Control: Oversee the quality assurance process to ensure the final packaging meets all standards of aesthetics, functionality, and durability.
- Troubleshoot Issues: Quickly identify and resolve any issues during the production process to avoid delays and extra costs.
3. Pre-Production Planning
Before manufacturing begins, detailed planning is essential to ensure the production process goes smoothly.
3.1. Review Design Files and Specifications
- Final Design Files: The design team will provide the production team with final, high-resolution design files, including:
- Artwork files: (e.g., .AI, .PDF) with all graphics, logos, and fonts used in the design.
- Dielines: Precise layout templates for cutting, folding, and assembling the packaging.
- Color specifications: Detailed color codes (Pantone, CMYK) for consistency in printing.
- Material Specifications: Detailed descriptions of materials, thicknesses, and finishes used in the design.
3.2. Material Sourcing and Availability
- Material Check: Confirm the availability of the selected materials (paperboard, plastics, glass, etc.) and ensure they meet quality standards.
- Sustainability Compliance: Verify that the materials comply with sustainability standards (e.g., recyclable, biodegradable).
- Lead Times: Review lead times for material procurement and ensure they align with production schedules.
3.3. Production Feasibility Review
- Cost Analysis: Recheck the budget and confirm that the material and production costs are within the agreed-upon financial parameters.
- Production Methods: Confirm the printing and manufacturing methods (e.g., flexographic, offset, digital) and ensure the production team is equipped and prepared to execute them.
- Testing of Materials: Ensure any new materials or techniques are tested for durability, usability, and safety before full-scale production begins.
4. Production Monitoring and Collaboration
Once production begins, the design and production teams must work closely to ensure everything runs smoothly.
4.1. Prototype Review and Approval
- Pre-Production Samples: The production team will create pre-production samples (also known as “pilot runs”) to ensure that the design translates well into the final packaging.
- Check for Accuracy: The design team reviews the pre-production sample to ensure all design elements are correctly implemented, including colors, logos, and structure.
- Functionality and Usability: Test the packaging for functionality, ease of use, and protection. For example, if the packaging includes closures, handles, or inserts, ensure they work as intended.
- Quality Check: Conduct quality checks for any potential issues, such as printing defects, color discrepancies, or material weaknesses.
4.2. Feedback and Adjustments
- Review Feedback: Once the pre-production sample is tested, gather feedback from the design team and other relevant stakeholders (e.g., marketing, product teams). If necessary, adjustments should be made based on the feedback.
- Tweak Designs: Minor revisions may be needed, such as color corrections, structural adjustments, or refinements to printing methods to meet quality standards.
4.3. Production Schedule Management
- Timeline Tracking: Stay in constant communication with the production team to track progress and ensure the packaging is produced on time.
- Production Milestones: Establish milestones throughout the production process, such as material procurement, sample approvals, and batch production runs, to monitor progress.
- Overcome Delays: Identify potential delays early and collaborate with the production team to mitigate them. For example, if materials are delayed, alternative sources or expedited shipping may be considered.
5. Quality Assurance and Control
Ensuring high-quality output is essential for maintaining brand standards and customer satisfaction. The design team should closely monitor the quality control process.
5.1. Quality Control Guidelines
- Consistency Checks: Ensure that the production team adheres to quality standards by performing routine checks for consistency in colors, print quality, and materials.
- Durability Testing: Conduct tests to evaluate the packaging’s durability, including testing its resistance to impact, moisture, temperature, and handling. For example:
- Drop tests for shock resistance.
- Compression tests for stacking or weight-bearing capabilities.
- Moisture tests for food or beverage packaging.
- Functional Testing: Verify that the packaging design performs as intended, including opening, resealing, and closure mechanisms (if applicable).
5.2. In-Line Production Inspections
- Inspection During Production: Regular inspections during the manufacturing process help identify any deviations from the design before too much product is produced.
- Random Sampling: Random samples can be pulled during each production run to verify that quality standards are being met.
5.3. Final Inspection
- End-of-Line Quality Control: Once production is complete, conduct a final inspection to ensure every batch meets SayPro’s standards. This includes checking for any last-minute imperfections or inconsistencies.
- Final Packaging Check: Ensure the finished product is packaged correctly, protected for shipping, and ready for distribution.
6. Post-Production Feedback Loop
After production, the design team and production team should engage in a feedback loop to ensure ongoing improvement and ensure that the packaging performs well in the market.
6.1. Market Feedback and Adjustments
- Customer Feedback: Gather feedback from customers and retailers about the packaging’s performance. Look for insights regarding ease of use, appeal, and any potential issues.
- Review Return Data: If products are returned due to packaging issues, review the packaging to identify areas of improvement.
- Continual Improvement: Use this feedback to make necessary adjustments for future production runs or to inform packaging design for new products.
7. Conclusion
The SayPro Production Collaboration phase is vital to ensuring that the finalized packaging design is executed perfectly, within the established timelines, and to the highest standards of quality. By working closely with the production team throughout the process—monitoring material procurement, pre-production samples, production runs, and quality control—SayPro ensures that the packaging will be both functional and visually appealing when it reaches the market. This collaboration helps minimize production issues, maintain consistency, and ultimately contributes to the product’s success on the shelves.
Leave a Reply
You must be logged in to post a comment.