Your cart is currently empty!
SayPro Quality Assurance: Ensure that all final designs are accurately reproduced in production and that the packaging is delivered to specifications on time.
SayPro is a Global Solutions Provider working with Individuals, Governments, Corporate Businesses, Municipalities, International Institutions. SayPro works across various Industries, Sectors providing wide range of solutions.
SayPro Email: info@saypro.online Call/WhatsApp: + 27 84 313 7407
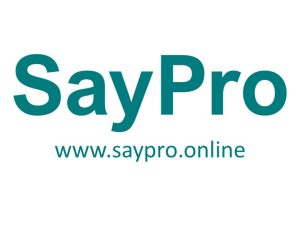
SayPro Quality Assurance: Ensuring Accurate Reproduction and Timely Delivery of Packaging
1. Introduction to Quality Assurance in Packaging:
Quality assurance (QA) is a crucial step in the packaging process, ensuring that SayPro’s final designs for the February SCMR-13 packaging are faithfully reproduced during production and meet all specified standards. QA involves a series of checks and balances at various stages of the production process to guarantee that the packaging is produced correctly, consistently, and in alignment with both the brand’s goals and environmental standards. From the design phase to final delivery, SayPro’s quality assurance process ensures that the packaging meets all customer, brand, and regulatory requirements, and is delivered on time and to specifications.
2. Key Aspects of SayPro’s Quality Assurance Process:
The quality assurance process at SayPro involves thorough planning, testing, and monitoring to verify that packaging designs are executed correctly and meet high-quality standards. Below are the core elements of the QA process:
a. Pre-Production Review and Approval:
Before production begins, it’s essential to ensure that all packaging designs are finalized and approved for manufacturing. This includes reviewing the artwork, specifications, and materials used to confirm that everything aligns with the desired outcome.
- Artwork and Design Review: The final design files (including graphics, text, and layout) should be carefully reviewed to ensure that there are no errors or inconsistencies. This review includes checking for color accuracy, font usage, alignment of logos and copy, and overall design cohesion.
- Material and Print Specifications: All materials chosen for packaging should be checked against specifications to ensure that the selected materials meet durability, aesthetic, and environmental standards. This includes reviewing the quality and sourcing of sustainable materials if applicable (e.g., recyclable or biodegradable options).
- Compliance with Brand Guidelines: The packaging should be evaluated against SayPro’s brand guidelines to ensure that it stays true to the company’s visual identity, messaging, and values. This may include verifying the use of correct colors, fonts, logo placement, and consistent visual style.
- Regulatory Compliance Check: Packaging must adhere to any relevant regulatory standards, including product labeling regulations, safety warnings, and any legal requirements regarding materials or messaging. This is especially critical for packaging in industries like food, cosmetics, or pharmaceuticals.
b. Prototype Testing:
Prototyping is a vital stage to ensure that the design is practical and achievable for mass production. Before full-scale production begins, creating and testing prototypes helps identify any potential issues with functionality, structure, or visual appeal.
- Prototype Creation: A sample or prototype of the packaging should be created using the same materials and production techniques that will be used for the final product. This prototype should be thoroughly inspected and tested to ensure that the design holds up under real-world conditions.
- Functional Testing: Prototypes should undergo functional tests to verify that the packaging performs as intended. This includes ensuring that it:
- Protects the product during transportation and handling.
- Is easy to open, reseal, or dispose of, depending on its design.
- Aligns with user experience goals, such as ergonomic design or usability.
- Visual and Structural Evaluation: The prototype should be evaluated for visual appeal, brand consistency, and structural integrity. Ensuring that the design looks appealing from a marketing perspective, while also being structurally sound to protect the product, is a key QA step.
- Feedback and Adjustments: Internal stakeholders, including product managers, marketing teams, and designers, should review the prototype. Any feedback provided during this stage should be used to refine the design, making necessary adjustments to meet both functional and aesthetic expectations.
c. Production Monitoring and Quality Control:
Once the prototype is approved, production begins, and ongoing monitoring is essential to ensure consistency and quality at every stage of the manufacturing process.
- Batch Testing and Sampling: During the production process, quality control personnel should regularly sample batches of packaging to test for consistency. These tests might include checking for:
- Material integrity (ensuring that materials used are of the correct type and quality).
- Print accuracy (confirming that color and text appear as expected on each batch).
- Structural integrity (verifying that the packaging holds up under typical use and shipping conditions).
- Production Line Inspection: QA inspectors should conduct on-site checks throughout the production run to monitor equipment performance, material handling, and packaging assembly. These inspections help detect and address any deviations from the specifications early, reducing the risk of faulty packaging reaching the final product stage.
- Packaging Functionality Checks: During the production process, functional tests should also be conducted on the packaging. For example, checking the ease of opening, closing, and resealing (if applicable), as well as ensuring the packaging protects the product from external damage or contamination.
d. Final Inspection and Approval:
Before packaging is shipped out for distribution, a final inspection is essential to ensure that every unit meets the required quality standards.
- Final Product Inspection: All completed packaging should undergo a final inspection process where it is checked for the following:
- Accuracy of design (confirming that the final product matches the approved designs and specifications).
- Material consistency (verifying that the materials used in production are of the correct grade, type, and quality).
- Structural integrity (ensuring that the packaging can withstand shipping, handling, and customer use without failure).
- Functionality and User Experience Testing: A final round of testing should be performed to ensure that the packaging is functional and provides a positive customer experience. This might involve stress tests (e.g., simulating transport conditions) and usability assessments.
e. Timely Delivery and Distribution:
Once the packaging passes all inspections and approvals, it’s important to ensure that it is delivered to the necessary distribution points on time and in the correct quantities.
- Production Timeline Management: Throughout the manufacturing process, SayPro’s team should carefully monitor production schedules to ensure that the packaging is completed and ready for shipment according to deadlines. This includes accounting for any potential delays in material sourcing or production bottlenecks.
- Logistics and Delivery Coordination: The QA team must collaborate with logistics to ensure that packaging materials are shipped on time and delivered to the right locations for final product assembly or retail distribution. Ensuring that the packaging is on time and intact is essential for meeting product launch timelines and customer expectations.
3. Tools and Technology for Quality Assurance:
SayPro can also leverage technology and tools to enhance the efficiency and effectiveness of the QA process:
- Automated Quality Control Systems: Implementing automated systems in production can help identify defects or variations in packaging production quickly. For example, cameras and sensors can be used to inspect print quality, material defects, or structural issues in real time.
- Digital Proofing Tools: Using digital proofing tools allows designers and stakeholders to review and approve packaging designs before physical samples are made. This helps reduce errors and unnecessary prototyping.
- Tracking and Reporting Systems: Software systems that track packaging production, inspections, and feedback can help streamline the QA process. These systems provide visibility into potential issues and enable teams to resolve problems quickly and efficiently.
4. Conclusion:
Quality assurance is essential in ensuring that SayPro’s packaging is accurately reproduced, meets design specifications, and is delivered on time. By implementing a robust QA process that includes pre-production reviews, prototype testing, ongoing monitoring during production, final inspections, and timely delivery, SayPro can ensure that its packaging for the February SCMR-13 issue meets high standards of quality, functionality, and aesthetics. A comprehensive quality assurance system not only reduces the risk of production errors but also helps maintain consistency across packaging, supports brand integrity, and enhances the customer experience. Ultimately, a well-executed QA process is integral to ensuring that SayPro’s packaging contributes positively to the overall product and brand success.
Leave a Reply
You must be logged in to post a comment.