Your cart is currently empty!
SayPro Quality Control Checklist
SayPro is a Global Solutions Provider working with Individuals, Governments, Corporate Businesses, Municipalities, International Institutions. SayPro works across various Industries, Sectors providing wide range of solutions.
Email: info@saypro.online Call/WhatsApp: + 27 84 313 7407
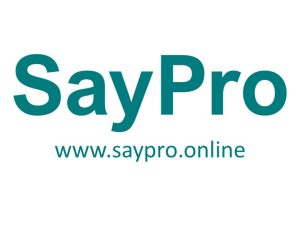
SayPro Monthly Printing: Ensuring the use of high-quality paper and printing for a premium product, managed by SayPro Brand Material Office under SayPro Marketing Royalty SCMR
SayPro Templates to Use: Quality Control Checklist
The Quality Control Checklist is an essential tool for evaluating the quality of printed materials before they are approved for distribution. It ensures that the printed materials meet SayPro’s high standards for color accuracy, resolution, and finish, maintaining a professional appearance consistent with SayPro’s brand. Below is a detailed breakdown of the Quality Control Checklist template and the key aspects to evaluate.
Quality Control Checklist for Printed Materials
1. General Information
- Print Order Number:
[Enter the unique reference number for the print order] - Date of Evaluation:
[MM/DD/YYYY] - Item Name/Description:
[Name/description of the printed material, e.g., “Brochure for Campaign X,” “Event Banner for Conference”] - Quantity Received:
[Total number of units received from the print vendor] - Vendor Name:
[Name of the print vendor] - Checked By:
[Name of the person conducting the quality control check] - Approval Status:
[Approved / Not Approved / Pending Review]
2. Color Accuracy
- Color Matching:
- Check that the colors on the printed material match the approved design/artwork file.
- Ensure that the colors are consistent with SayPro’s brand guidelines (e.g., logo color, primary colors, etc.).
- Pantone/CMYK Consistency:
- Verify that Pantone or CMYK values used in the print job are accurate, especially for brand-specific colors.
- Print Variations:
- Inspect the print run for any variations in color (e.g., lighter or darker tones than the approved sample).
- Confirm that color inconsistencies do not appear across different units of the same print material.
3. Resolution and Image Quality
- Image Sharpness:
- Ensure all images and graphics are clear and sharp, with no pixelation or blurring.
- Resolution:
- Check that the resolution of images is appropriate (e.g., 300 DPI for printed materials).
- Clarity of Text and Graphics:
- Verify that all text is legible, clear, and sharp, with no fuzziness or distortion.
- Print Overlaps:
- Look for any misalignments or overlaps in printed text or images that can cause visual distortions.
4. Paper and Material Quality
- Paper Weight:
- Check the paper weight against the specifications (e.g., 100gsm, 200gsm) to ensure it matches the order details.
- Paper Texture:
- Confirm that the paper texture (e.g., glossy, matte, or textured) aligns with the approved specifications.
- Paper Finish:
- Verify that the finish (e.g., gloss, matte, UV coating) matches what was requested in the print order.
- Paper Quality Consistency:
- Ensure that the quality of the paper is consistent across all units, with no visible defects (e.g., rough edges, bends, or tears).
5. Print Alignment and Layout
- Margins and Bleed:
- Check that all materials have the correct margins and proper bleed area, ensuring there are no white borders where there should be color.
- Text and Image Alignment:
- Ensure that all text and images are aligned according to the design specifications (e.g., text should not be cut off at edges).
- Fold/Crease Alignment (if applicable):
- Check that folds and creases are even and crisp, with no misalignment in brochures or pamphlets.
- Cutting Accuracy:
- Inspect the cut edges for straightness and precision; there should be no uneven cutting or frayed edges.
6. Finish and Special Features (If Applicable)
- Lamination or Coating:
- Verify that any lamination or coating (e.g., gloss or matte finish) is applied evenly across all materials without bubbles, creases, or streaks.
- Embossing or Debossing:
- Check that any embossing or debossing is done cleanly, with clear impressions and no defects.
- UV Coating or Spot UV:
- Inspect any UV coating for smoothness, even coverage, and proper application in the specified areas.
- Binding (If Applicable):
- Verify that any binding, such as stapling, saddle stitching, or perfect binding, is secure and clean, with no loose pages or misalignment.
7. Packaging and Delivery
- Packaging Integrity:
- Ensure that the printed materials are packaged securely to prevent damage during transit (e.g., no crushing or bending of items).
- Labeling and Identification:
- Verify that the packaging is clearly labeled with the order number, item name, and quantity for easy identification.
- Correct Quantity Delivered:
- Cross-check the number of units delivered against the quantity requested in the order.
- Delivery Condition:
- Ensure that the materials are delivered in good condition, with no visible damage, smudges, or dirt on the printed surfaces.
8. Final Approval and Comments
- Final Quality Check Status:
- Approved: All printed materials meet the required quality standards and are ready for distribution.
- Not Approved: Materials do not meet the required standards, and a reprint or adjustment is necessary.
- Pending Review: Further review is required by the Brand Material Office or another department before approval.
- Additional Comments or Issues:
[Provide any specific feedback on issues found during the quality control check (e.g., “Color mismatch on Page 3,” “Paper quality is lower than expected,” etc.)]
Purpose and Usage of the Template
The Quality Control Checklist is designed to:
- Ensure Consistency and Professionalism: It helps ensure that every printed item meets SayPro’s professional quality standards, maintaining a consistent and high-quality brand image.
- Identify Issues Early: By carefully evaluating each printed material, potential issues such as color discrepancies, poor resolution, or finishing defects can be identified and addressed before distribution.
- Document the Evaluation Process: The checklist serves as a record of the quality control process, making it easy to track issues and provide feedback to print vendors or internal teams.
- Support Decision Making: The checklist provides clear insights into whether the printed materials are ready for distribution or if revisions are necessary.
This template should be used by the SayPro Brand Material Office under the SayPro Marketing Royalty SCMR program to ensure that all printed materials are thoroughly evaluated for quality before they are used in marketing campaigns, events, or other professional applications.
Leave a Reply
You must be logged in to post a comment.